Gauge Fillet Weld Fundamentals: Finest Practices and Common Mistakes
Gauge Fillet Weld Fundamentals: Finest Practices and Common Mistakes
Blog Article
Cutting-edge Strategies to Fillet Weld Assessment and Screening: Enhancing Weld Quality and Compliance Requirements
In the realm of welding, the quality and stability of fillet welds play a critical function in making sure the structural stability and integrity of various industrial elements. With the consistent drive for boosted efficiency and conformity with rigorous requirements, the expedition of innovative approaches to fillet weld evaluation and testing has actually become critical. As markets advance, the standard methods may no more suffice in fulfilling the demands of modern welding applications (Gauge Fillet Weld). By embracing advanced technologies and methodologies, a new perspective of opportunities emerges in the realm of weld top quality analysis and adherence to compliance requirements.
Advanced Non-Destructive Screening Techniques
Utilizing state-of-the-art technologies, advanced non-destructive screening techniques play a crucial duty in making certain the integrity and quality of fillet welds. These techniques, such as phased selection ultrasonic testing (PAUT) and magnetic fragment testing (MPT), deal comprehensive understandings into the weld's inner structure without creating any damages to the product. PAUT, for instance, makes use of multiple ultrasonic aspects to inspect the weld from different angles, providing a comprehensive visualization of prospective issues like lack of blend or cracks.
In A Similar Way, MPT is effective in finding surface-breaking defects by applying an electromagnetic field and iron particles to the weld area. This method is specifically useful for determining discontinuities that may endanger the weld's toughness. By employing these sophisticated non-destructive testing methods, weld assessors can properly assess the quality of fillet welds, making certain compliance with industry requirements and guidelines. The ability to detect imperfections beforehand not only enhances weld high quality yet additionally prevents expensive rework or failures in structural integrity, underlining the importance of these ingenious testing techniques in welding inspections.
Robotics and Automation in Assessment

The assimilation of robotics and automation has transformed the evaluation procedure for fillet welds, improving effectiveness and precision in top quality assessment. Robotics offer precise control and repeatability in evaluating welds, making certain regular and trusted outcomes. Automated systems can be programmed to adhere to specific examination paths, guaranteeing detailed protection of welds and reducing the threat of human error.
Robotic examination systems geared up with sophisticated sensing units can discover and gauge weld features with high precision, supplying thorough data for analysis. These systems can recognize problems such as fractures, absence of fusion, and porosity, allowing punctual corrective actions to be taken. Furthermore, robotics and automation enable real-time data collection and analysis, offering instant responses to operators and assisting in quick decision-making processes.
Moreover, making use of robotics and automation in fillet weld inspection improves total performance by reducing evaluation times and raising inspection throughput. By improving the assessment procedure, producers can make sure weld high quality and compliance requirements are satisfied effectively, eventually resulting in cost savings and improved product quality.
Making Use Of Expert System for Evaluation
Expert system plays a crucial duty in enhancing the efficiency and precision of analysis in fillet weld evaluation processes. By taking advantage of the power of AI, examiners can simplify the evaluation of weld high quality and compliance standards, resulting in extra dependable and specific outcomes. AI algorithms can quickly refine substantial quantities of data from weld evaluations, identifying issues or variances that may be testing to understand the naked eye. This innovative modern technology enables real-time surveillance of weld quality, permitting instant corrective actions to be taken if any type of problems are detected.
Moreover, AI systems can gain from previous assessment information, continually enhancing their capability to determine possible defects and discrepancies in fillet welds. This flexible learning capability enhances the total high quality control procedure, minimizing the chance of human error and ensuring that welds fulfill the needed criteria. By incorporating expert system into fillet weld evaluation, markets can attain higher degrees of efficiency, consistency, and conformity in their examination practices.
Portable Tools for On-Site Inspection
Enhancing field evaluation effectiveness, the adoption of portable tools transforms on-site evaluation processes for fillet welds. These tools offer flexibility and benefit, enabling examiners to carry out thorough examinations in various locations, consisting of tough or remote try this web-site settings. Portable devices such as ultrasonic screening devices, magnetic particle examination equipment, and digital radiography systems give real-time data and high-resolution imaging abilities, making it possible for quick decision-making and immediate responses on weld top quality.
One substantial advantage of portable devices is their ability to streamline evaluation procedures, decreasing downtime and improving overall productivity - Gauge Fillet Weld. Assessors can quickly transfer these tools to various task sites, eliminating the demand for carrying heavy machinery or parts to off-site centers. Additionally, the portability of these tools advertises cost-effectiveness by lessening transportation expenditures and speeding up assessment timelines
Furthermore, using mobile tools for on-site examination advertises aggressive top quality control steps, as inspectors can quickly identify and deal with any kind of possible welding problems or discrepancies. By including these look these up cutting-edge technologies into on-site evaluation practices, welding professionals can ensure compliance with market requirements and enhance weld high quality, ultimately resulting in boosted structural stability and safety in different welding applications.
Combination of Data Monitoring Solution
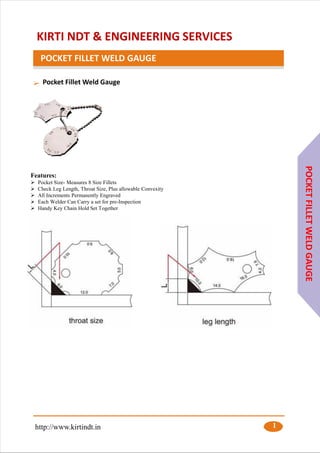
Having maximized on-site assessment processes via the utilization of portable devices, the next stage entails the seamless assimilation of data management systems to additionally improve efficiency and information evaluation capacities in fillet weld evaluation and testing. By incorporating information monitoring systems into the inspection procedure, organizations can enhance data collection, storage space, and analysis. This combination permits real-time tracking of weld quality, instant identification of flaws, and prompt decision-making to remedy any kind of issues that may emerge throughout the assessment procedure.
Data monitoring systems play an important function in centralizing assessment information, promoting easy accessibility for authorized workers, and making certain data stability and safety. With the assimilation of these systems, examiners can produce thorough reports, track historic information for fad analysis, and boost total process effectiveness. Furthermore, the combination of data administration systems allows smooth communication between different stakeholders included in the assessment process, cultivating collaboration and improving general top quality control measures. Eventually, the assimilation of information administration systems offers to elevate the requirements of fillet weld inspection and screening, guaranteeing conformity with sector policies and improving weld quality.
Final Thought
Finally, cutting-edge techniques to fillet weld examination and testing have significantly boosted weld high quality and compliance criteria. check this Advanced non-destructive testing approaches, robotics, automation, fabricated intelligence, mobile devices, and data monitoring systems have transformed the means weld evaluations are conducted. By utilizing these innovations, industries can make certain that welds fulfill the needed top quality requirements and laws, ultimately boosting overall performance and security in welding procedures.

Having maximized on-site evaluation procedures with the usage of portable devices, the next phase involves the smooth integration of information administration systems to better boost effectiveness and data evaluation abilities in fillet weld examination and testing. Ultimately, the assimilation of data monitoring systems serves to raise the standards of fillet weld evaluation and testing, ensuring conformity with industry guidelines and boosting weld quality.
Report this page